ATEC’s PARAFORMALDEHYDE
TECHNOLOGIES
ATEC is in
possession of technologies to produce all
types of Paraformaldehyde products in varying concentration ranges and
polymerization degree spans. It can offer PLANTS for:
(89-91)%
FLAKED PARAFORMALDEHYDE PRODUCTION
Multi stage evaporation
and chilled conveying process.
(91-96)%
GRANULAR / PRILLED PARAFORMALDEHYDE PRODUCTION
Multi stage evaporation
and rotary vacuum drying.
(91-96)%
PRILLED PARAFORMALDEHYDE PRODUCTION
Multi stage evaporation
and spray cum fluidized bed drying.

PARAFORMALDEHYDE PLANTS
PLANTS
for production of flakes are relatively inexpensive, whereas the processes for
production of prills / granules are
fairly elaborate and such PLANTS involve a much larger investment.
Paraformaldehyde
is a polymer of Formaldehyde in solid form, containing a percentage of
water, readily soluble in order to obtain an aqueous solution or to be used as
a reactant by dissolving it in the reaction medium.
Paraformaldehyde,
which is represented by typical formula HO
(CH2O)n H is
also termed as mixture of Polyoxymethylene Glycols. It is controlled polymerized product of
Formaldehyde in solid form. The presence
of Formaldehyde unit per molecule is more than 6.
PARAFORMALDEHYDE
PRODUCTS RANGE
Typical characteristics of various Paraformaldehyde
grades known to be manufactured are given below:
FREE
FLOWING WHITE GRANULES WITH TYPICAL FORMALDEHYDE ODOUR (Granules)
|
WHITE
POWDER
|
89%
|
91%
|
93%
|
96%
|
97%
|
FORMALDEHYDE
CONTANT (%)
|
89
± 1
|
91
± 1
|
93
± 1
|
95.5
± 1
|
96.5 ± 1
|
METHANOL
CONTENT (%Max.)
|
1
|
0.5
|
0.5
|
0.5
|
0.5
|
pH (10%
AQUEOUS SUSPENSION
|
3-5
|
3.5-6.5
|
3.5-6.5
|
5-7
|
5-7
|
ACIDITY (AS
FORMIC ACID (%) Max.)
|
0.03
|
0.03
|
0.03
|
0.03
|
0.03
|
REACTIVITY
(RESORCINOL TEST ) (Minutes)
|
2-3
|
2-4
|
2-4
|
2-4
|
3-5
|
FLASH POINT
(OPEN CUP) (oC)
|
93
|
93
|
93
|
93
|
93
|
FLASH POINT
(CLOSED CUP) (oC)
|
71
|
71
|
71
|
71
|
71
|
IRON CONTENT
(PPM Max.)
|
2
|
2
|
2
|
2
|
2
|
ASH CONTENT
(PPM Max.)
|
100
|
100
|
100
|
100
|
100
|
MELTING POINT
(oC)
|
120-170
|
120-170
|
120-170
|
120-170
|
120-170
|
BULK DENSITY
(kg / m3)
|
750-750
|
750-850
|
750-850
|
750-850
|
500-800
|
GRAIN SIZE
(MIN. 80%) (mm)
|
|
|
0.2-1.0
|
0.2-1.0
|
0.2-1.0
|
0.2-1.0
|
Min. 90% < 0.100 DIN 60
|
PRODUCTION TECHNIQUE
Production of Paraformaldehyde usually starts
from 37% or 55% by weight aqueous
solutions of Formaldehyde. It is concentrated at temperatures below 100°C often
done by vacuum distillation and mainly water distills of at first. The
concentration of Formaldehyde present chiefly as hydrate is increased. The
solutions can be concentrated in this way up to Formaldehyde content of above
80% at which point the greater part of the Formaldehyde is already present in
the form of oligo – oxymethylene glycols. On cooling, gels with colloidal
properties are obtained which are at first waxy but later on becomes brittle
which consist of Paraformaldehyde.
ATEC`s FLAKED
PARAFORMALDEHYDE TECHNOLOGY
Paraformaldehyde in
flake form is produced by this process.
The raw material for the said Paraformaldehyde production is freshly
manufactured high concentration (52-55%) Formaldehyde solution. A basic flow
diagram is given below :
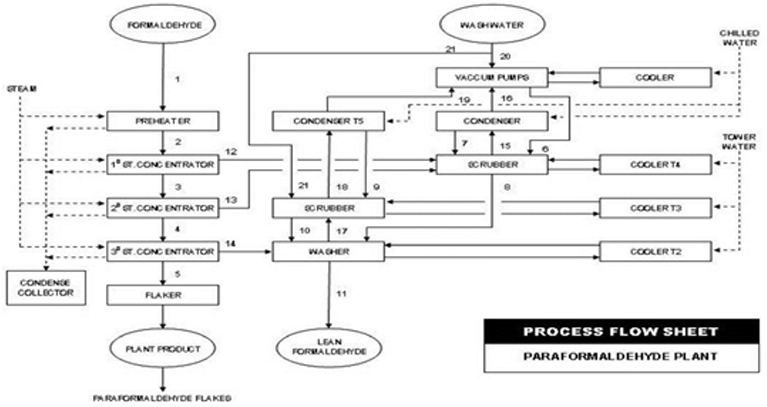
Salient
Features
Salient features of ATEC`s modified process for
manufacture of flaked Paraformaldehyde are enumerated below:
1)
Simple in Operation
2)
Free flowing, dustless
white flakes. Dust is a big problem for the workers handling Para
3)
100% utilization of
Formaldehyde with almost ‘0%’ loss in the process.
4)
100% pollution free
5)
Highest safety measures
6)
Easy solubility and
simple to dissolve
7)
Low power consumption
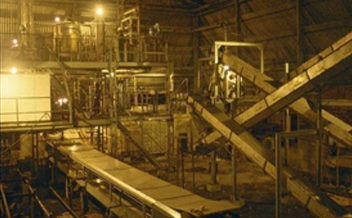
FLAKED
PARAFORMALDEHYDE PLANTS
GRANULAR
/ PRILLED PARAFORMALDEHYDE PRODUCTION TECHNOLOGY BY ROTARY VACUUM DRYING
A unique process based on Vacuum Concentrated and Drying of Product
to produce various (91% to 96%) concentration grades of Paraformaldehyde would
be applied. In the ATEC process Paraformaldehyde is manufactured from aqueous
(37%) Formaldehyde solutions by the process involving distillation and
concentration at a point at which solidification or precipitation of polymer
takes place. The process of concentration is carried out by vacuum evaporation.
The main sections of the PLANT are:
Concentration of aqueous
Formaldehyde (AF-37 / AF-55)
Polymerization and
drying
Concentration of
distillates for recycling.
Conveying,
pulverization and storage / packaging of the Product.
This Process is offered by ATEC in association with Libra Techcon.
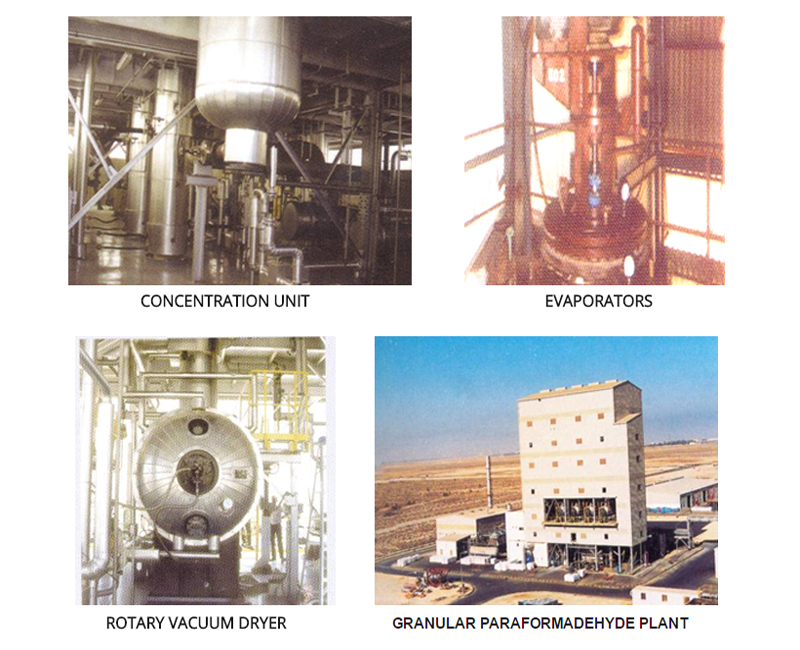
Indicative Process flow diagram for the Granular / Prilled Paraformaldehyde
processes is shown below:
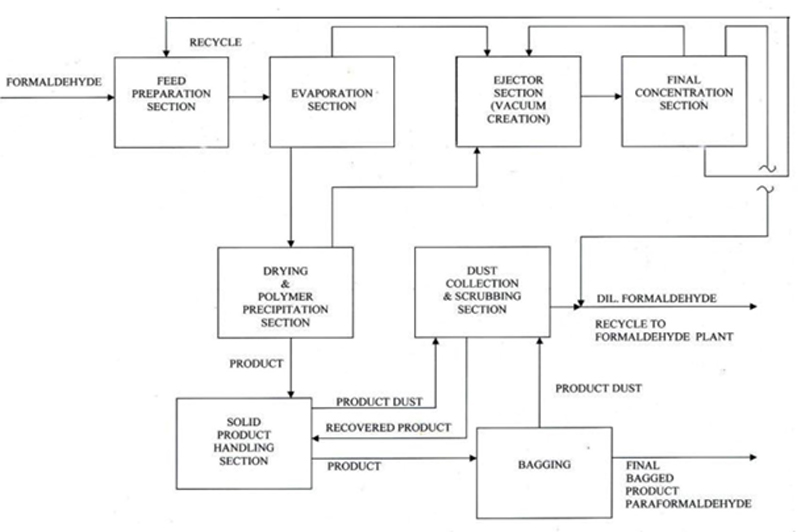
GRANULAR / PRILLED PARAFORMALDEHYDE PROCESSES BASED ON ROTARY VACUUM DRYING
The Process has been over the years upgraded based on actual operational experience obtained in
PLANTS of different optimal production level from 5 M.P.D through 15 M.T.P.D.
upto 30 M.T.P.D. and beyond. The upgradation carried out was in terms of optimization
of equipment / machinery sizing and more compact lay out at individual floor
level of the PLANTS.
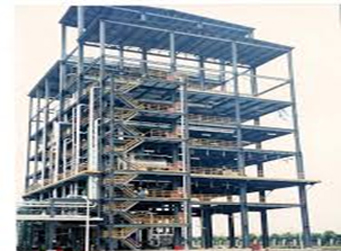
PARAFORMALDEHYDE PLANTS
PRILLED
PARAFORMALDEHYDE PRODUCTION PROCESS BASED ON SPRAY CUM FLUIDIZED BED DRYING
The process essentially consists of the following
steps:
·
Concentration of
Aqueous Formaldehyde
·
Vacuum Spray Drying
·
Fluidized Bed Drying
·
Product Handling
Concentration of Aqueous
Formaldehyde (AF-37) to AF (75 – 85) is carried out in a falling film
evaporation and thin film evaporation (side stream) system.
(75 – 85) % concentrated Aqueous
Formaldehyde is fed to a conical bottom NIRO vacuum Spray Dryer.
Spray dried powder is further
concentrated in a Fluidized Bed Dryer before being sent to the product handling
system. A liquid catalyst is used.
Three different grades (89%, 92%
and 96%) of Paraformaldehyde are produced by under for end use application in
resins, agro chemicals (Herbicides / Pesticides), Disinfectant / Medical
intermediates sectors.
Basic block diagrams of the Process
are shown below:
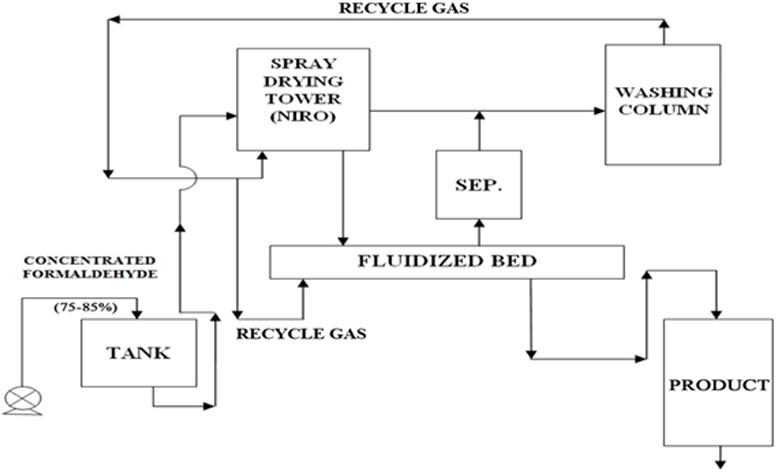
PROCESS
BLOCK DIAGRAM
ALTERNATIVE
PRILLED FORMALDEHYDE PROCESS
An alternative process for production of
prilled Paraformaldehyde products
using the “Prilling Tower Concept” is
also available. A schematic block
diagram of this Process is shown below:
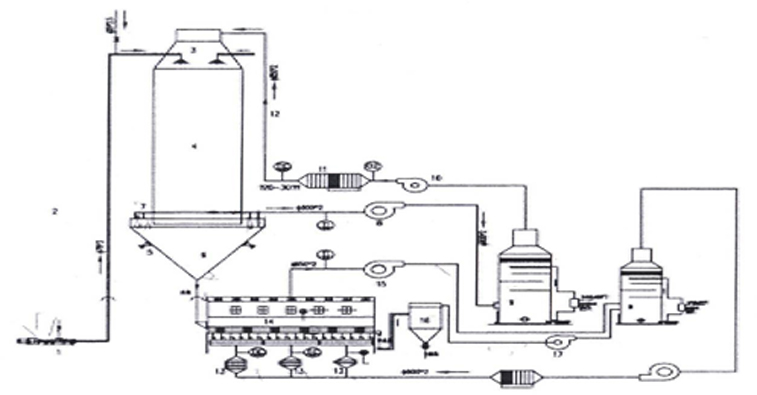
SCHEMATICS
OF PRILLED PARAFORMALDEHYDE PRODUCTION
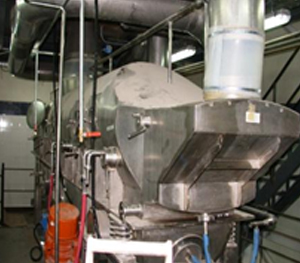
COMBINED
SPRAY AND FLUIDIZED BED DRYING FOR PARAFORM
PRODUCT’S
SPECIFICATIONS
The granular Paraformaldehyde manufacturing processes offered by ATEC
will produce Paraformaldehyde of the
following specifications:
Aldehyde
content (as HCHO % by mass)
|
:
|
(91-96
± 1) for individual grades
|
Ash
Content, ppm (max.)
|
:
|
100
|
Free
Moisture content Percent by mass, (max.)
|
:
|
1
|
Acidity
(as HCOOH) Percent by mass (max.)
|
:
|
0.03
|
Iron
(ppm by mass max)
|
:
|
2
|
p-H
|
:
|
4
– 7
|
Methanol
(% by mass max.)
|
:
|
1
|
Melting
Point
|
:
|
120º
- 170º C
|